What's the Sheet Metal Forming Press
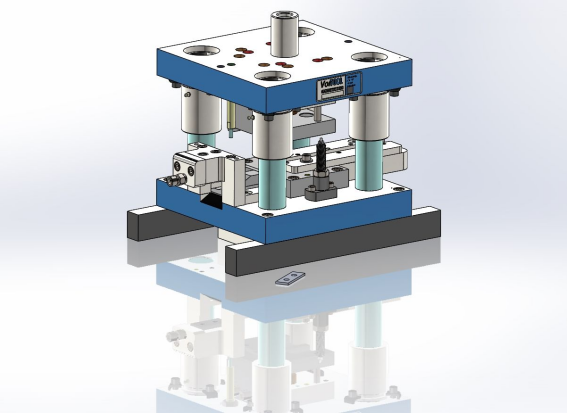
Definition: Sheet metal forming press dies are the tools that shape and cut sheet metal parts. They are commonly developed using computer-aided design (CAD) software and analytical programs to create and prove-out highly accurate, unambiguous designs. These designs are then translated into stamping dies by skilled craftsmen, known as die makers.
Different Kinds of Press Die Under the Different Classifications
Classification according to the process nature
Item | Photo | Description |
Punching die | (a) Die stages. (b) Stages of punching | A die that separates materials along a closed or open contour line. Such as drop die, punching die, cutting die, notching die, cutting edge die, cutting die, etc. |
Bending die | The die that makes the sheet blank or other blanks along the straight line (bending line) to produce bending deformation, so as to obtain a certain angle and shape of the piecework. | |
Deep drawing die | It is the die that makes the sheet blank into an open hollow part or makes the hollow part further change its shape and size. | |
Forming die | It is a die that directly copies and forms the blank or semi-finished piecework according to the shape of the convex and concave die, while the material itself only produces local plastic deformation. Such as expansion die, indentation die, flaring die, undulation forming die, clanging die, shaping die, etc. | |
Riveting die | It is to borrow external force to make the participating parts connected or lapped together in a certain order and way, and then form a whole. |
Classification according to the degree of process combination
Simple die
Definition: A die that completes only one stamping process in one stroke of the press.
Application: It simply accepts the catheter and punches a few slots in it
Advantage:Simply: Convenient to use alone, convenient for punching small metal plates.
Compound die
Definition: A die that has only one work station and completes two or more stamping processes at the same work station in one stroke of the press.
Application:
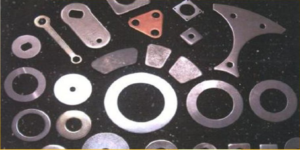
Advantage:High production rate: Only one component should be stroked.
Progressive die
Definition: A die that has two or more stations in the feeding direction of the blank and completes two or more stamping processes at different stations one after another in one stroke of the press.
Application: Progressive die stamping is used to produce a large number of parts, and maintain the lowest cost as possible. It also need to meet the required precision and durability.
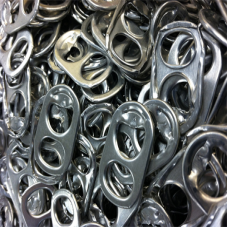
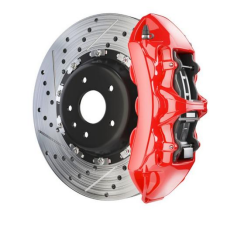
Advantage:
Synchronization: The production speed is the same as the production speed of the composite mold.
Force reduction: By providing shear or by staggered stamping methods, the force required will be reduced.
Ease of operation: The design and manufacture of punch and die combinations is easier because the operations are carried out in different stages, regardless of the number of operations.
Transfer die
Definition: It combines the characteristics of single process die and progressive die, and uses robotic transfer system to achieve rapid in-die transfer of products, which can greatly improve the production efficiency of products, reduce the production cost of products, save material cost, and have stable and reliable quality.
Application: This can be a single die on its own or multiple dies arranged in a continuous station. Versatile, many part features such as piercing, chauffeuring, notching, ribbing, knurling and threading can be designed into the primary stamping process without adding additional cost to many secondary processes.
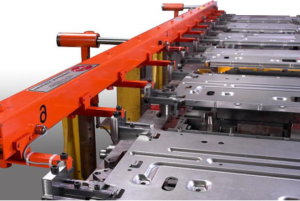
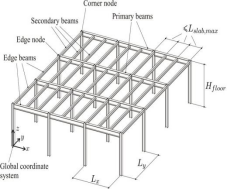
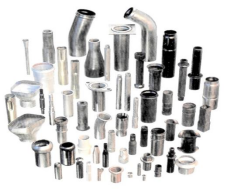
Advantage:
Cost-effective: More economical production compared to progressive die.
High level of automation: Large parts will be handled and transferred between multiple presses to complete the operation.
Multiple Dies
Definition: Multiple dies also known as gang dies ate those dies which produce tow or more pees at each stroke of press. In these dies a number of simple dies are ganged together to produce tow or more parts via each stroke of the press.
Application: For example, in order to produce 10 washers in each stroke, 10 compound molds or 10 progressive molds are stored in parallel, called multiple dies.

Advantage:
High productivity: More components are produced due to the presence of more molds.
Combination Die
Definition: Combination dies are used for operations that involve multiple operations at one workstation. In these dies, the cutting operation is combined with a bending or drawing operation, hence the name “combination die”.
Application:
Advantage:
High productivity: Since cutting and forming operations are performed simultaneously on the working material, the productivity is much higher compared to other molds.
Conclusion
Since the 1990s, the rapid development of automobile, home appliances, communications and other industries, and at the same time also led to the rapid development of the die industry. In the international development of the die requirements is very obvious. The future development of press die technology should be “fast delivery”, “high precision”, “high quality”, “low price ” as the requirement standard.
Die design level and manufacturing level is also a measure of the country’s manufacturing capacity, so to a very large extent on the quality of products, efficiency and new product development capabilities are playing a decisive role.