Classification by drive method:
Manual press brake
Manual press brake is now gradually eliminated from the market, it is suitable for small sheet metal processing thin plate
The manual clamping system is an effective, economical, press brake fixture for infrequent tool changes. Manual clamping of the tooling is the most basic and time-consuming clamping method, requiring the bending operator to manually lock each clamping plate. The individual clamping plates do not automatically form a complete clamping line when locked one by one, the clamping force is not uniform for each section of the die, the die is not immediately aligned, time-consuming to set up and dependent on an experienced operator.
Hydraulic press brake
Usually, press brake for the upper piston type press, by the frame, slider, hydraulic system, front bracket, backstop, mold, electrical system and other parts.
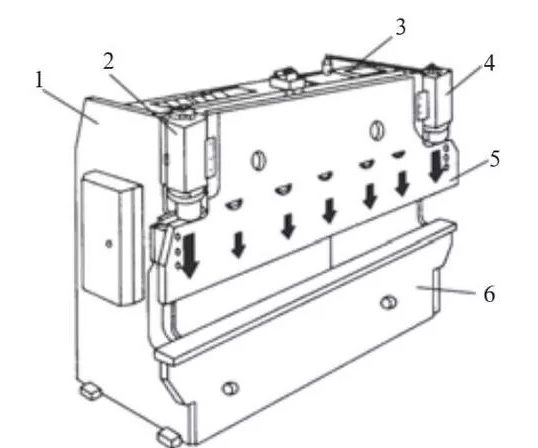
A vertical downward pressure is formed by two working hydraulic cylinders moving in parallel to drive the tooling on the bending beam for bending work. The hydraulic control system, as the brain of the press brake, mainly controls the synchronous operation of the bending process and the positioning of the hydraulic cylinders when the machine is working at full load.
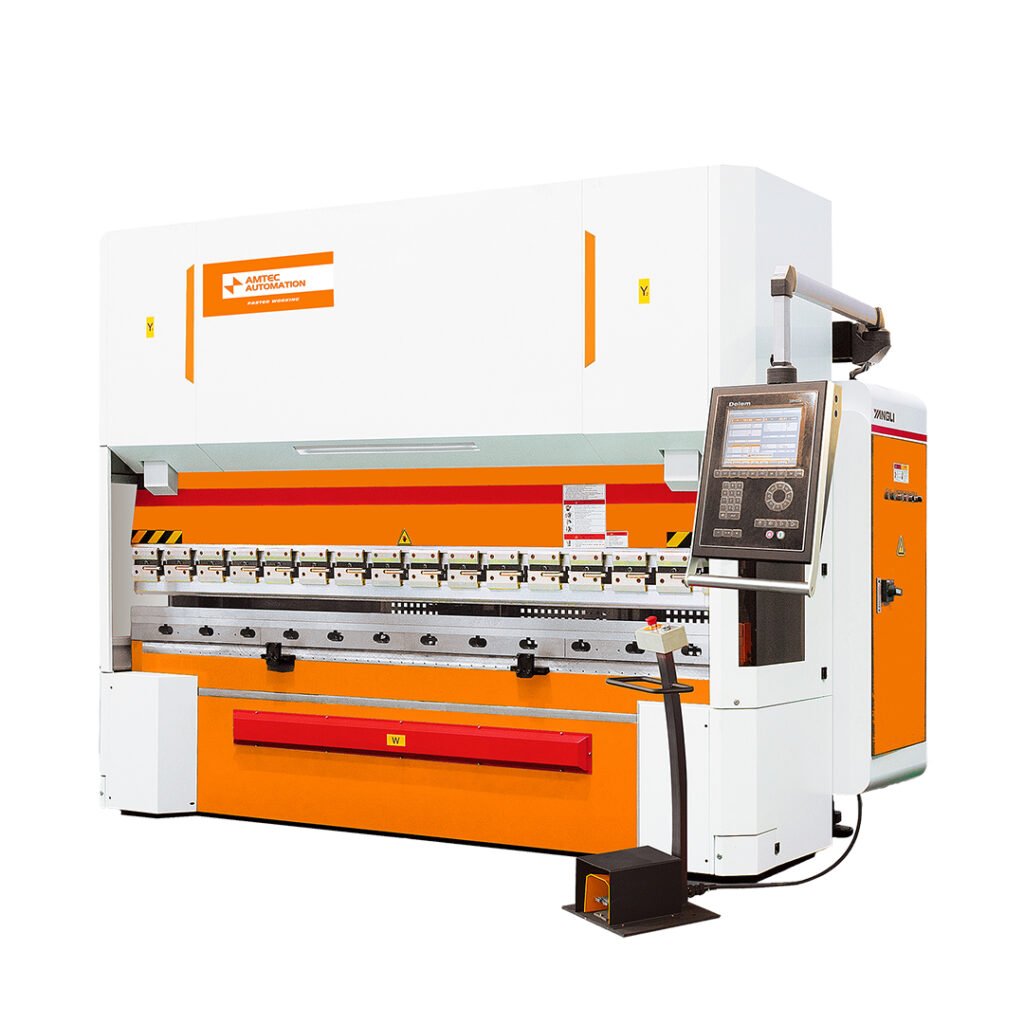
Hydraulic system development trend:
Hydraulic system development, while promoting the rapid development of the machine tool industry, in order to adapt to the hydraulic system to high performance, high precision and automation direction development needs, CNC hydraulic technology, elector-hydraulic servo technology and other new hydraulic technology is also developing rapidly, from the current state of research, hydraulic system development trend will be reflected in the following areas:
(1) modern hydraulic technology and microelectronics technology, computer control technology, sensor technology and other new technologies represented by the close combination, the formation and development of an automation technology including transmission, control, detection.
(2) The combination of digital electronics and hydraulic technology.
(3) Miniaturization.
(4) Greening to reduce energy consumption, leakage control, and pollution control.
synchronous operation of the bending process and the positioning of the hydraulic cylinders when the machine is working at full load.
Electric Press Brake
The electric press transmits power through two synchronous servo motors, and presses with the help of special belts and pulleys. When the upper beam moves downward, the servo motor winds the belt onto the main pulley and applies bending force. The return force is mechanical, it comes from springs located on both sides of the machine. After bending, the servo motor starts to de-ice the belt, and the spring pushes the upper beam to the TDC position of the program. In the electric brake, the photoelectric protection device is closely connected with the control device, so that the light curtain or similar device has no influence on the bending cycle time.
In fact, in the field of electric press brakes, safety does not necessarily need to sacrifice cycle time. In hydraulic systems, the tonnage (downward force) comes from hydraulic drives on both sides of the machine. This means that when the slider drops, touches the metal piecework, and encounters resistance, the press brake will bend. This creates the well-known deflection, which is usually handled by some type of coronal system. For example, in a pulley-driven electric press brake, an AC servo motor drives a dual pulley system that extends the length of the press brake column. The number of pulley blocks varies according to the size and power requirements of the machine. The belt is made of 0.12-inch thick steel wire reinforced material, coated with polyurethane, the same as that widely used in elevator systems.
Classification by control method:
CNC press brake
CNC press brake is designed for cold-rolled sheet metal processing sheet metal forming machinery, widely used in automotive, aircraft manufacturing, light industry, shipbuilding, containers, elevators, railway vehicles and other industries of sheet metal bending processing.
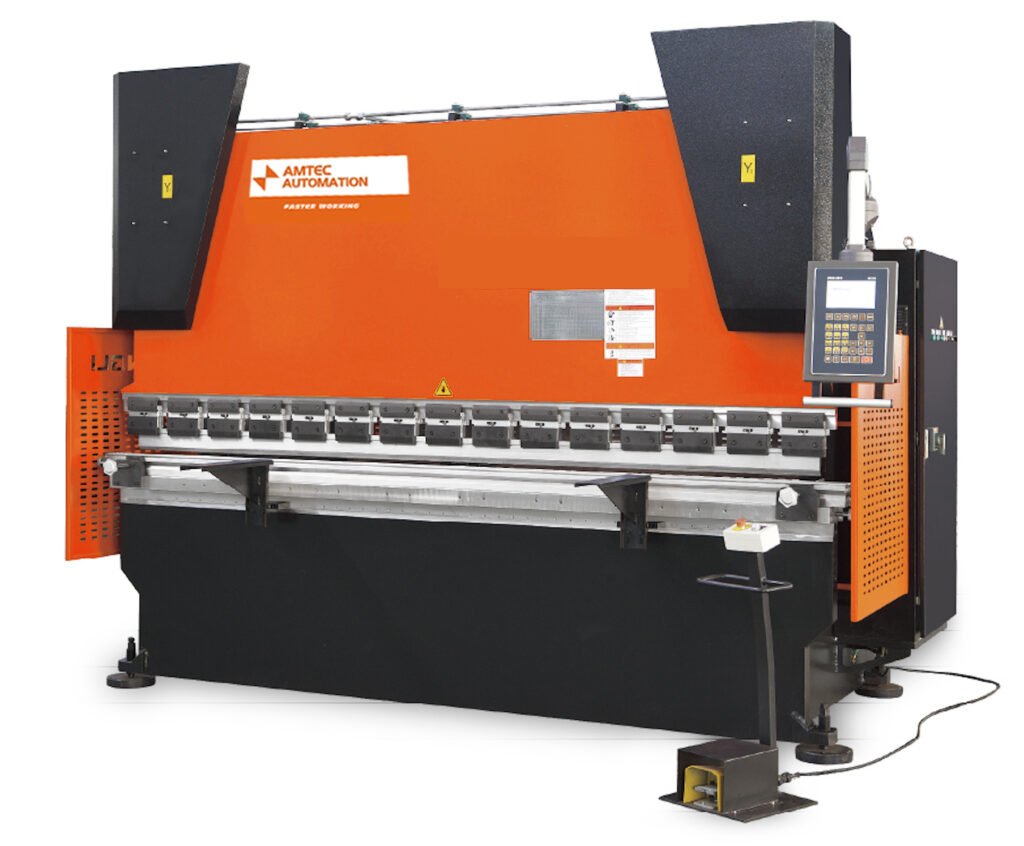
Main Components:
Slide:

Hydraulic transmission is adopted, and the slider part consists of slider, oil cylinder and mechanical stopper fine-tuning structure. The left and right oil cylinders are fixed on the frame, and the piston (rod) is driven up and down by hydraulic pressure to move the slider, and the mechanical stopper is controlled by CNC system to adjust the value.
Working table:
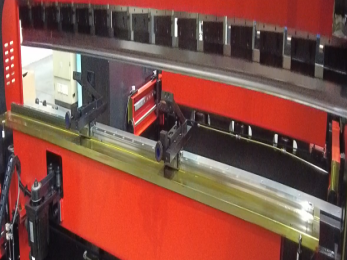
Manipulated by the button box, so that the motor drives the blocking frame to move back and forth, and the distance of movement is controlled by the CNC system, and its minimum reading is 0.01mm (the front and rear positions are limited by the travel switch).
Synchronization system:
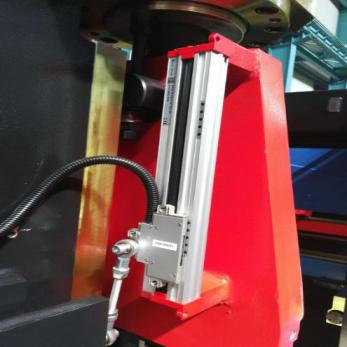
The machine is a mechanical synchronization mechanism composed of twisted shaft, swing arm, joint bearing, etc. with simple structure, stable and reliable performance and high synchronization accuracy. The mechanical block is adjusted by the motor and the numerical control system controls the value.
Blocking mechanism:
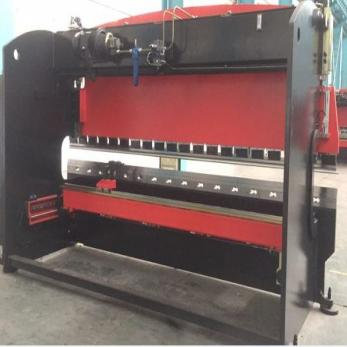
The blocking material is driven by motor, through the chain operation drives the synchronous movement of the two filaments, the CNC system controls the size of the blocking material. Laser processing system combined with computer numerical control technology can constitute an efficient automatic processing equipment, for high quality, efficient and low-cost processing production opened up a broad prospect.
Advantages of CNC press brake:
With the advances in science and technology of the times press brake introduced elector-hydraulic servo synchronization technology to complete the press brake grade, the advantages of CNC press brake are mainly in the following areas.
- The use of elector-hydraulic servo system control double-cylinder synchronization, with the international standard of the scale, the formation of a full closed-loop control, synchronization control precision, bending accuracy, repeatability also reached a very high level.
- Can be equipped with hydraulic upper die automatic clamping device or fast clamping device, slot type lower die according to user needs, reduce the labor intensity of workers and improve production efficiency.
- Equipped with segmented upper die of different lengths, which can be assembled into a certain width according to the requirements of the piecework, in order to adapt to the processing needs of special piecework.
- CNC cylinder deflection automatic compensation system to overcome the impact of slider deformation on the quality of the piecework during the work process, ensuring good straightness and bending angle of the processed piecework.
- Flexible operation mode can be adopted, both double machine linkage to solve the processing of extra-long plates and single machine operation to process short pieces, which improves the utilization rate of machine tools and reduces energy consumption.
- The body is welded with steel plate and clamped at one time and processed by CNC five-sided machining center as a whole, which ensures extremely high rigidity of the body and processing accuracy.
Conventional Press Brake
Although ordinary press brakes are not as advanced as CNC machines, they can also meet the needs of most customers.
Destruct and features of Amtec conventional press brake:
1)The frame adopts the whole welded structure, the whole is tempered by the fireplace, the accuracy of the machine is well maintained.
2)Double-cylinder structure, hydraulic up-motion type, sleepless pressure regulation. High quality imported seals and brand-name hydraulic and electrical components are used to ensure the reliability of the machine.
3)Mechanical synchronization, the use of adjustable compensation structure of oblique chisel, to improve the machining accuracy of the parts.
4)The machine tool has a point, single, continuous operation specifications and pressure-holding function, commutation, pressure-holding time can be controlled through the time relay.
5) The electrical box is equipped with an open-door power-off device, which improves the safety of operation.
Take model APA-40/2500 as an example:
Type | Description | specification |
| |
1 | Nominal force | 400 | kw | |
2 | Length of table | 2500 | mm | |
3 | SPN | ≥16 | min-1 | |
4 | Between columns | 2000 | mm | |
5 | throat depth | 200 | mm | |
6 | Slide stroke | 100 | mm | |
7 | Max.open height | 330 | mm | |
8 | Stroke adjustment | 80 | mm | |
9 | Overall dimensions (L×W×H) | Long | 2710 | mm |
Wide | 1250 | mm | ||
High | 2240 | mm | ||
10 | Net weight | 3075 | kg | |
11 | Main motor power | 4 | kw |
Conclusion
In recent years, the domestic CNC press brake has developed rapidly, even available in English for human-machine dialogue, programming, bending force calculation and control of bending force, equipped with a display screen, after entering the size of each analysis can display the analysis of the monochrome image of the product, display the calculated analysis of the vow program and bending images of each process, intuitive tips for the operator how to operate.
With the rapid development of digital control technology and the increasing perfection of servo motor technology, as well as some users have higher requirements for material surface quality and are more sensitive to oil leakage of hydraulic drive press brakes, mechanical servo press brake has been used and developed in these industries. Therefore, the foreign market appeared mechanical servo press brake . Domestic users of this type of demand is gradually increasing, but also can take advantage of the low domestic manufacturing costs, the product into the international market, on the one hand, to increase the scale of production and marketing, on the other hand, export earnings. The emergence of servo drive technology on the CNC sheet press brake plate processing is a revolution. Our production of press brakes are: CNC elector-hydraulic servo synchronous press brake, high-speed type CNC press brake, CNC elector-hydraulic servo synchronous press brake and equipped with manipulators, fully automated CNC press brake for your choice, its high precision is favored by many people, they can be mobile and flexible operation, effectively improve the use rate, reduce energy consumption, compensation by the CNC system automatically adjusted, convenient and accurate.