Warning!
When we use the CNC turret punch press, try to reduce the number of opening the motor cabinet at the CNC turret punch processing site, because the air at the processing site contains a lot of oil mist, dust, and even metal powder, etc. These metal powders are scattered on the circuit boards or electronic components of the control part of our CNC turret punch press, which is very easy to cause the insulation resistance of the components to decrease, and may even cause damage to the components and circuit boards of the CNC turret punch. For the customers of our CNC turret punch press, I would like to remind you that there should be strict regulations in the factory. Unless necessary adjustments and maintenance are required, it is not allowed to open the door of the electrical cabinet at will, and it is not allowed to open the cabinet when using the equipment.
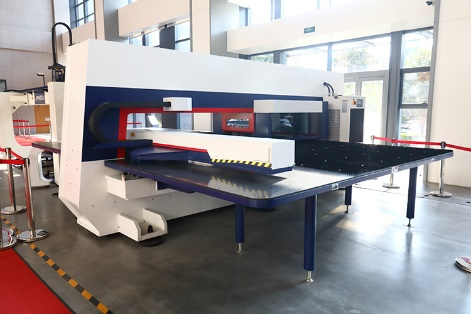
8 tips needing attention in the maintenance of CNC turret punch die
- Ensure the best mold gap. The mold gap refers to the sum of the gaps on both sides of the punch entering the lower mold. Different plate thicknesses and different materials should be used for lower molds with different clearances. Choosing a suitable mold gap can ensure good punching quality, reduce burrs and collapse, keep the sheet flat, effectively prevent stripping, and extend the life of the mold.
Due to the pressure and heat during punching, the small particles of the sheet material will be bonded to the surface of the punch, resulting in poor punching quality. It can be polished with fine oilstone to remove the sticky material, and the polishing direction should be the same as the direction of the punch movement.
If a lot of holes are punched on a board, you should punch every other hole first, and then return to punch the remaining holes, which effectively alleviates the stress accumulation during sequential punching in the same direction, and will also make the front and back two sets of holes The stresses cancel each other out, thereby reducing the deformation of the sheet.
Try to avoid punching narrow strips. When the die is used to punch a sheet with a width less than the thickness of the sheet, the punch will bend and deform due to lateral force, which will make the gap on one side too small or aggravate the abrasion. In severe cases, it will scratch the lower die and cause the upper and lower dies. Damaged at the same time.
Timely sharpening can effectively extend the service life of the mold. When the die edge wear produces a circular arc with a radius of about 0.10 mm, sharpening is required. When sharpening, the grinding amount is 0.03~005mm each time, and the grinding is repeated until the punch is sharp. After sharpening, use oilstone to polish the cutting edge to remove burrs, and apply lubricating oil after demagnetization.
Regularly check the alignment of the upper and lower mold bases of the turntable. If the center of the punch die position is not good, the die will be quickly passivated and the processing quality of the work piece will deteriorate. Check and lubricate the die holes and guide keys on the turntable. If damaged, repair and clean the lower die seat of the turntable in time, so that the lower die can be installed accurately, and check the wear of its keys or key grooves, and replace them if necessary; use a special mandrel for calibration If there is any deviation, adjust the mold station in time.
When punching soft or viscous materials (such as aluminum); punching thin abrasive materials (such as glass epoxy sheet); punching thin hard materials (such as stainless steel); frequently nibbling, you can use surface hardening (using plating Titanium, chlorine infiltration and other methods, the surface hardened layer is a punch with a thickness of 12-60um molecular structure).
The molding die should be fine-tuned upwards from the lowest position to the appropriate position, otherwise the die will be easily broken.